Adaptive Molds
Digital systems that reconfigure to form 3D shapes at speed and scale.
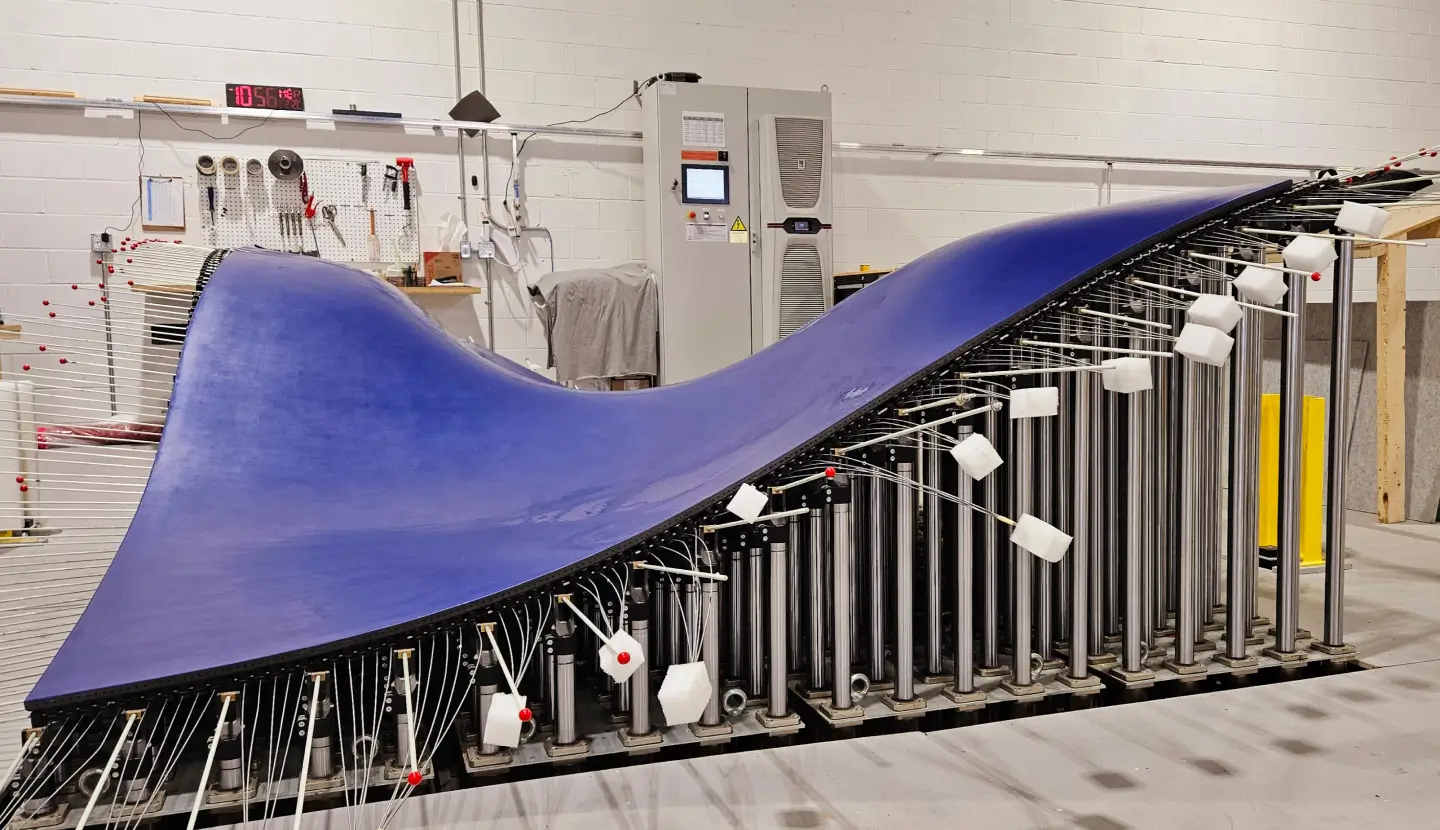
Rapid Production Speed
Less than 5 min. from CAD file to 3D surface. No lead time.
Scalability
One mold can produce thousands of unique parts, not dependent on manpower.
Sustainability
Eliminates materials, energy and waste of building, storing and disposing of traditional molds.
Versatility
Can be used for thermoforming, hand layup and vacuum infusion processing of composites using thermoset and thermoplastic materials.
Adapa For Composites Molding
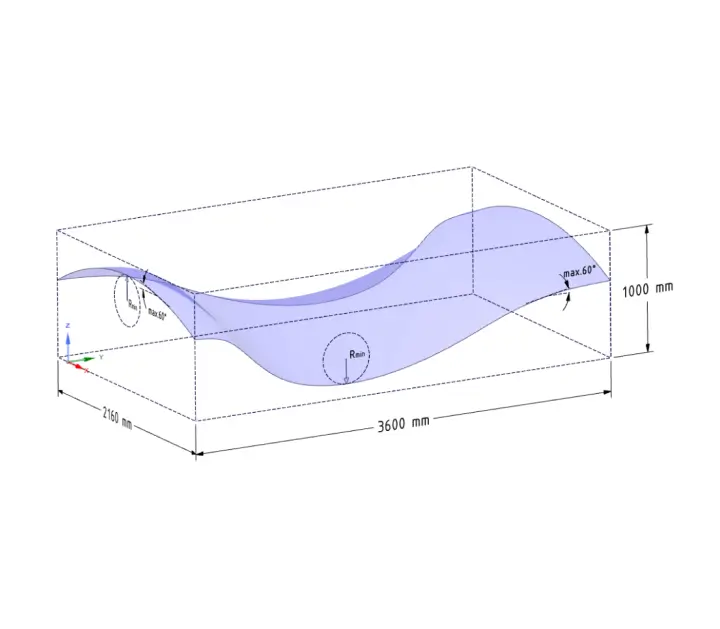
Three basic size and minimum curvature radius options feature molding surfaces capable to 140°C, but systems can also be customized to meet specific requirements.
Three basic size and minimum curvature radius options feature molding surfaces capable to 140°C, but systems can also be customized to meet specific requirements.
D100
- Min. radius 400 mm
- Max. area 2160 x 3600 mm
- Tolerance ± 1.5 mm
- Max. payload 280 kg/m2
D200
- Min. radius 900 mm
- Max. area 3400 x 5400 mm
- Tolerance ± 2.0 mm
- Max. payload 225 kg/m2
D300
- Min. radius 1800 mm
- Max. area 3600 x 5400 mm
- Tolerance ± 2.5 mm
- Max. payload 225 kg/m2
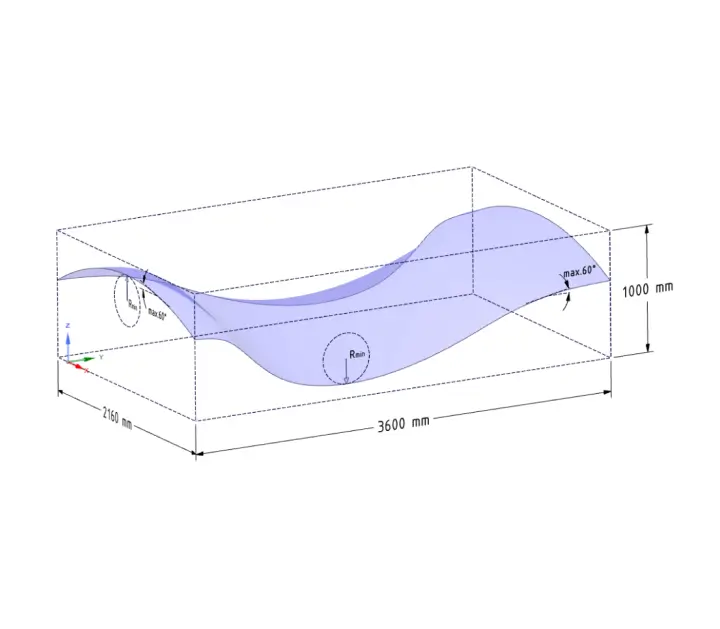
Process Flexibility
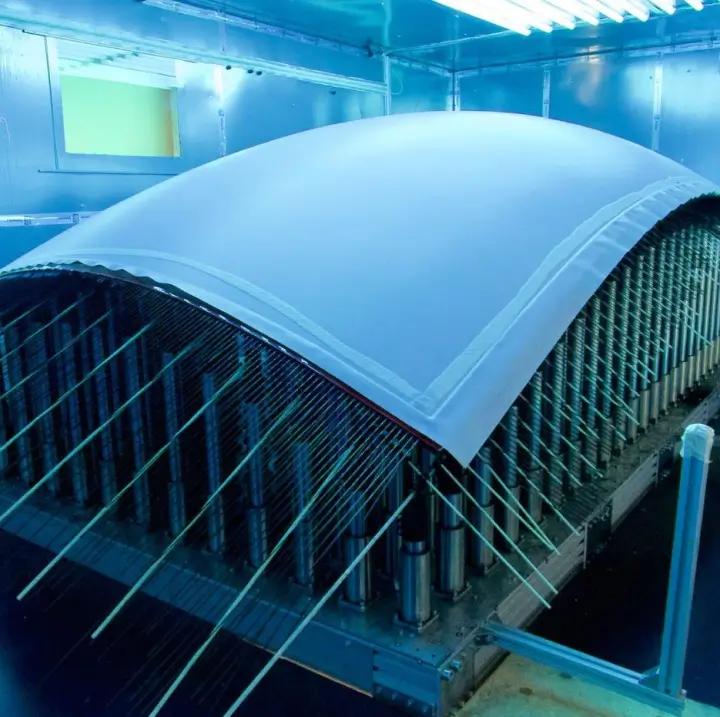
Adapa adaptive mold systems accommodate a wide range of processes while maintaining 3D shape precision.
Adapa adaptive mold systems accommodate a wide range of processes while maintaining 3D shape precision.
Range of Materials
Wide range of materials can be processed including thermoset and thermoplastic prepregs as well as dry fibers with epoxy, polyester, vinylester or acrylic resins. Foam cores and other thermoplastic materials can be vacuum and/or thermoformed.
Collaborative Technologies
Collaborative technologies that can be used with adaptive mold systems include:
- Layup guidance via laser projection systems.
- Heating via portable ovens, IR lamps and heat blankets/mats.
- Vacuum systems for resin infusion processes.
- Edge precision via magnetic silicon sides and shuttering for variable panel/part sizes.
- Top membranes for molding patterns or inlays.
- Robotic layup or finishing processes.
Adapa Tools Software
Adapa Tools software is an easy-to-use plugin to Rhino3D that transfers CAD files to the adaptive mold. Input or select panel/part shapes and then verify the geometry for production tolerances. The software also included a guided process to account for springback.
Additional requirements can be added as well as options such as:
- Which side faces the mold
- Laser projection lines to be shown
- Panel thickness
- Panel name and edge numbering
Multi-stage Molding/Forming
Multi-stage molding/forming is possible by laying up materials while the mold is flat and then activating it to the desired 3D shape. The molded panel is then released by selectively lowering system actuators.
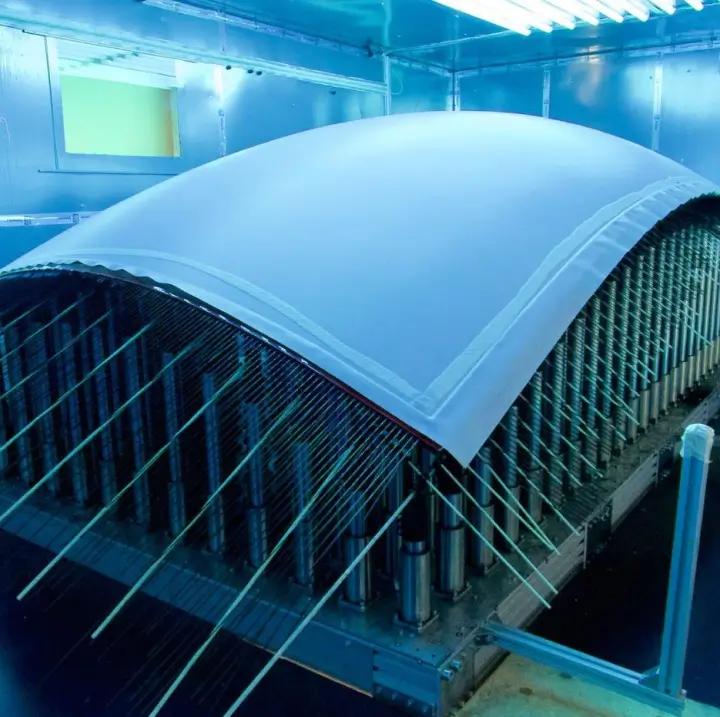